Advanced Welding WPS: Tailoring Specifications for Facility Tasks
Advanced Welding WPS: Tailoring Specifications for Facility Tasks
Blog Article
Unlocking the Power of Welding WPS: Techniques for Efficiency and Safety in Fabrication
In the realm of manufacture, Welding Treatment Requirements (WPS) stand as the foundation of welding procedures, dictating the required steps for achieving both performance and safety and security in the manufacture process. Understanding the details of WPS is critical to harnessing its full possibility, yet several companies have a hard time to unlock real power that lies within these records (welding WPS). By diving into the strategies that maximize welding WPS, a globe of improved productivity and enhanced security waits for those ready to explore the subtleties of this essential element of fabrication

Significance of Welding WPS
The importance of Welding Treatment Specs (WPS) in the construction market can not be overemphasized. WPS act as an important roadmap that outlines the essential actions to ensure welds are performed consistently and properly. By defining crucial specifications such as welding processes, products, joint designs, preheat temperature levels, interpass temperatures, filler steels, and post-weld warm therapy demands, WPS provide a standard approach to welding that improves efficiency, high quality, and safety in construction processes.
Adherence to WPS assists in attaining uniformity in weld top quality, decreasing the chance of flaws or architectural failures. This standardization additionally facilitates conformity with sector policies and codes, making certain that produced frameworks meet the needed safety and security standards. Additionally, WPS documents enables welders to duplicate effective welding procedures, resulting in regular results throughout various projects.
Fundamentally, the thorough development and stringent adherence to Welding Procedure Specs are extremely important for upholding the stability of bonded frameworks, safeguarding against prospective dangers, and maintaining the track record of fabrication companies for supplying high-grade services and products.
Crucial Element of Welding WPS

Enhancing Efficiency With WPS
When maximizing welding procedures, leveraging the essential elements laid out in Welding Treatment Specs (WPS) becomes crucial for taking full advantage of and improving procedures productivity. One way to enhance efficiency with WPS is by thoroughly selecting the proper welding parameters.
Furthermore, appropriate training and accreditation of welders in understanding and implementing WPS can additionally boost performance. Guaranteeing that all group members are fluent in translating and executing the WPS properly can reduce errors and rework, saving both time and sources. Frequently reviewing and upgrading the WPS to include any type of lessons learned or technical advancements can likewise add to effectiveness renovations in welding operations. By accepting the standards stated in the WPS and constantly looking for methods to maximize processes, makers can accomplish greater performance levels and remarkable end results.
Ensuring Safety And Security in Manufacture
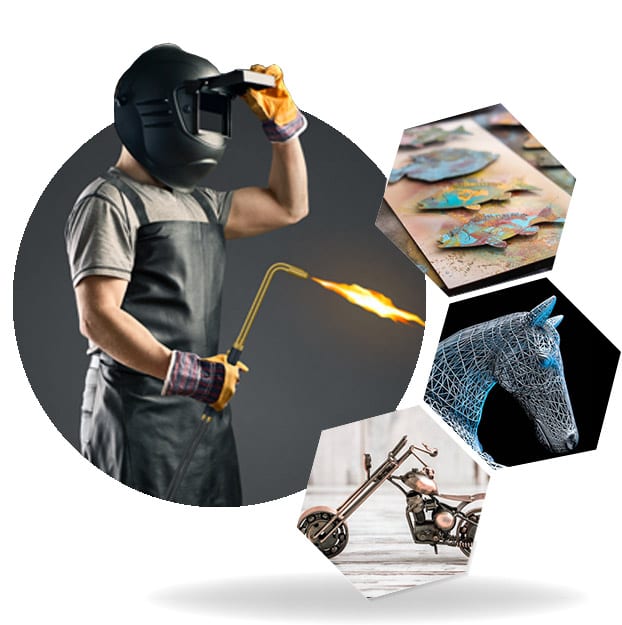
Safety and security protocols in fabrication play a pivotal duty in guarding workers and enhancing operational treatments. Making certain security in fabrication entails a complex technique that encompasses different elements of the welding process. One basic element is the arrangement of personal safety devices (PPE) customized to the certain risks present in the construction environment. Welders must be outfitted with proper equipment such as safety helmets, handwear covers, and safety clothing to minimize dangers related to welding tasks.
Additionally, adherence to appropriate Read Full Report air flow and fume extraction systems is vital in maintaining a healthy and balanced workplace. Welding fumes have damaging materials that, if inhaled, can present serious health and wellness risks. Implementing efficient air flow steps assists to decrease direct exposure to these hazardous fumes, promoting breathing wellness among workers.
Normal equipment maintenance and evaluations are additionally important for making sure safety and security in fabrication. Defective equipment can bring about injuries and accidents, highlighting the relevance of regular checks and timely repair work. By prioritizing precaution and cultivating a culture of awareness, fabrication facilities can produce a safe and effective work environment for their personnel.
Executing WPS Best Practices
To improve functional performance and make certain top quality end results in fabrication processes, integrating Welding Treatment Requirements (WPS) ideal techniques is paramount - browse this site welding WPS. Executing WPS ideal methods includes careful preparation, adherence to sector criteria, and continual surveillance to guarantee optimal results. First of all, selecting the suitable welding process, filler material, and preheat temperature specified in the WPS is essential for achieving the desired weld high quality. Secondly, making sure that qualified welders with the needed qualifications perform the welding treatments according to the WPS standards is crucial for uniformity and integrity. Routinely updating and assessing WPS records to show any procedure enhancements or changes in materials is additionally a crucial best technique to preserve accuracy and importance. Furthermore, providing thorough training to welding workers on WPS requirements and ideal methods cultivates a culture of security and high quality within the fabrication setting. By faithfully carrying out WPS best practices, makers can improve their procedures, reduce mistakes, and provide superior products to fulfill client assumptions.
Verdict
To conclude, welding WPS plays a critical role in making sure efficiency and safety in construction procedures. By concentrating on key aspects, boosting performance, and implementing ideal practices, business can maximize their welding operations. It is necessary to focus on precaution to stop accidents and make sure a smooth manufacturing procedure. By following these techniques, companies can open the complete capacity of welding WPS in their helpful site construction procedures.
In the world of manufacture, Welding Treatment Specs (WPS) stand as the backbone of welding operations, dictating the necessary actions for attaining both performance and security in the construction process. By specifying crucial parameters such as welding processes, materials, joint designs, preheat temperature levels, interpass temperatures, filler metals, and post-weld heat therapy needs, WPS supply a standardized approach to welding that enhances effectiveness, high quality, and safety and security in fabrication procedures.
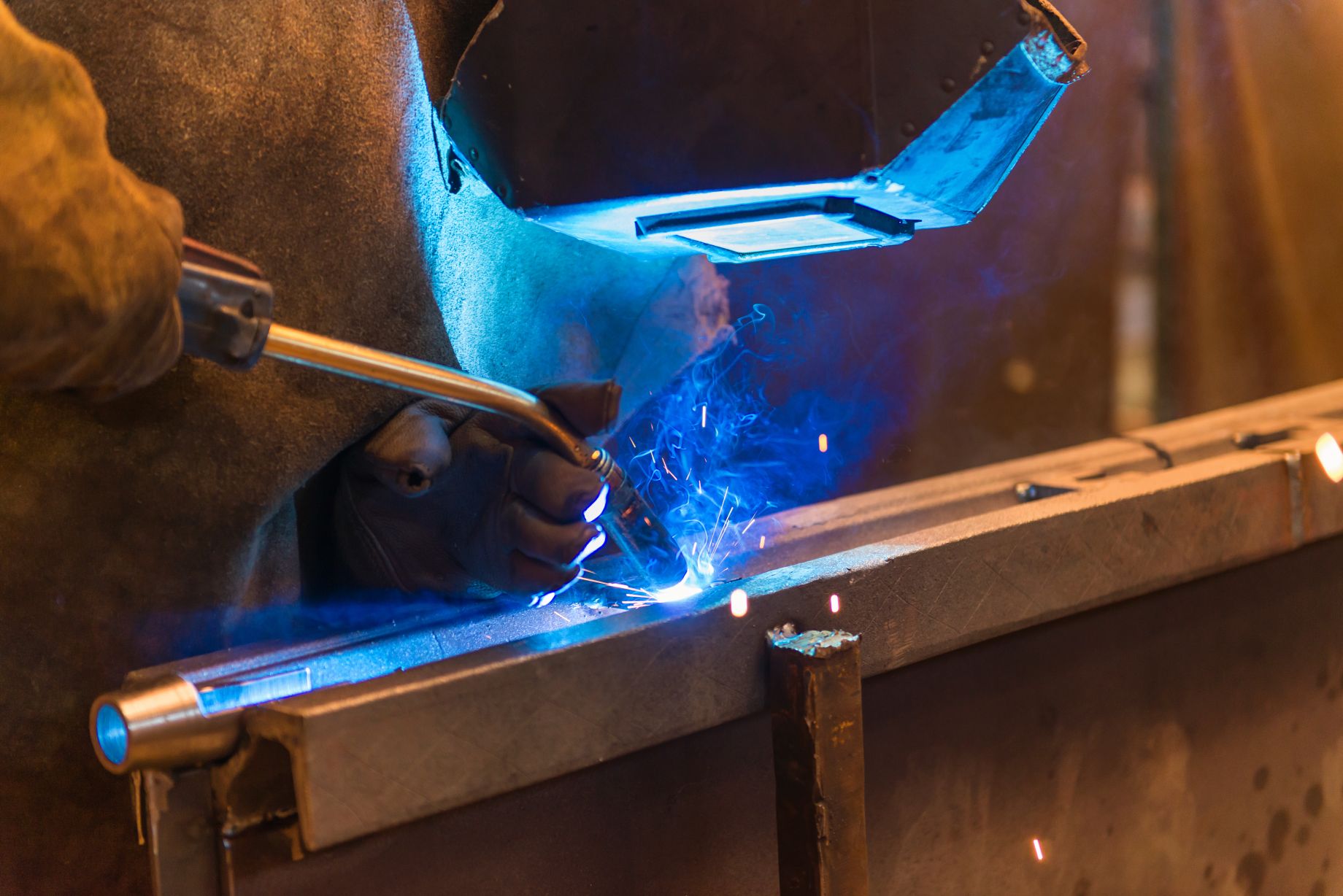
When optimizing welding operations, leveraging the crucial components described in Welding Treatment Requirements (WPS) comes to be vital for making the most of and improving processes performance. (welding WPS)
Report this page